New Systems for Vehicle Design by MANRM
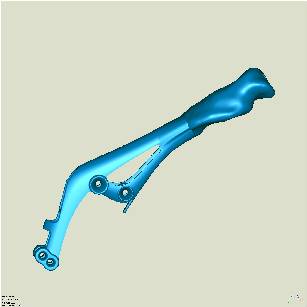
An automotive handbrake designed using rapid manufacturing techniques
2004-10-09 - Leicestershire, England: Advances in Rapid Manufacturing could ultimately allow motorists to help design and personalise details of their vehicle at a local dealer, according to an ongoing British research project.
MANRM - Management, Organisation and Implementation of Rapid Manufacturing - is the result of a research consortium under the Foresight Vehicle initiative, a Government-funded programme aimed at keeping Britain ahead in high-technology in the automotive sector.
Rapid Manufacturing (RM) offers the potential to alter the methods by which vehicle components are manufactured and allows opportunity for the production of detailed parts at low cost and at locations away from the conventional factory. Such a scenario is the base car being produced at the manufacturer's factory and then individual parts 'personalised' by the distributor, retailer or the customer at a different site. Potentially, the 3D profile of the client could be 'scanned-in' at a dealership's RM machine and then the custom parts could be created, and fitted, on-site.
Unlike current manufacturing methods where material is either removed (machining) or the moulding of materials is made in a tool (injection moulding), RM works on the principal of adding material. This build method removes constraints around design and allows the production of almost any geometry.
As a result of RM, manufacturers will have their production costs dramatically reduced - no tooling is required - and customers will enjoy enhanced product satisfaction from a personalised item that is reasonably priced.
MANRM aims to investigate how the advent of RM - which is already used by many Formula One teams and those involved in the creation of specialist vehicles - will affect the manufacture of medium to low volume and custom vehicle manufacture. Plus, it will also work to counter industry's concerns of the cost of RM production and material properties.
Under the banner of the Rapid Manufacturing Research Group (RMRG), experts at Loughborough University have been conducting the project for the last year with assistance from industry partners: JCB Research, The Engineering Forum, MG Rover, Mitre Group, Ford Premier Automotive Group, Perkins Engines and Martin Baker Aircraft Ltd.
Dr Richard Hague, head of the Rapid Manufacturing Research Group, believes RM will have a significant impact on the future of the automotive industry. He says: "The need to meet the demand for personalised products, particularly within the automotive sector, is growing increasingly important. RM offers the solution and benefits all parties involved. It is essential to embrace the technology offered by RM and maximise its potential to develop the future of automotive manufacturing."
Main areas of study have centred on the analysis of tooling costs, the identification of components on a vehicle that are suitable for RM, the development of a technology test bed, the impact of Rapid Manufacturing on small and medium-sized enterprises, a make or buy analysis and the location at which RM could take place.
At the end of the programme's three-year study period, MANRM will return a definitive report on the requirements for a future RM system and in two years will have created a 'road map' of the future of RM for SMEs.
Via an audit of components supplied by partner companies, the project has already highlighted vehicle parts suitable for RM. These have been progressed with the aid of existing Rapid Prototyping technology and costed using a full cost method developed on the project. Although not economic for the production of components, Rapid Prototyping has allowed MANRM to define areas for attention when considering next generation RM systems.
In the main, interior components have been pinpointed as being viable for RM - generally where they are either hidden under a dashboard or covered in a different material, such as leather. With the properties, and the varieties, of materials progressing, it is expected that more and more components will become suitable for RM in the future.
In addition, a breakthrough method has been developed for the production of customised seating with input from Martin Baker Aircraft Ltd. The RMRG technology test bed has been used to develop bespoke seats for combat aircraft trainee pilots in the British RAF that will increase pilot comfort over extended mission times. Whilst only a concept at the moment, the method of data capture and production using a mix of 3D Scanning, CAD and RM demonstrates the possibilities of RM for customised manufacture and importantly, body-fit products.
The technology involved in creating body-fit products allows the findings of MANRM to touch other industries as well as automotive and aerospace. Possible body-fit products include prostheses, seating and medical implants. Other areas identified by RMRG that could benefit from Rapid Manufacturing are sports equipment, consumer goods and protection equipment.
More than 400 UK companies and universities have been participating in the industry-backed initiative, known as Foresight Vehicle, led by the UK Society of Motor Manufacturers and Traders (SMMT).
|